CCA is a specification utilized in the battery industry to determine a battery's capacity to start an engine in freezing temperature ranges. In most cases, it is simpler to start the motor engine in a warm atmosphere compared to a cold one. The rating appertains to the amount of amps a 12-volt battery can easily supply at 0°F for Half a minute while sustaining a voltage of a minimum of 7.2 volts. The bigger the CCA rating, the higher the starting power of the battery.
The cold cranking amp estimator explained in this article is a test device designed to provide you with a realistic estimation of the battery's energy potential.
Although Cold Cranking Estimator is not a truly accurate device, it can save you from getting left behind in a drastic conditions. Both the data of relative power vs. temperature (Fig. 1) and the GW BASIC listing (Listing 1) may, together with an understanding of the atmospheric temperature, provide you with a dependable idea of your battery's cold cranking ampere (CCA) status.
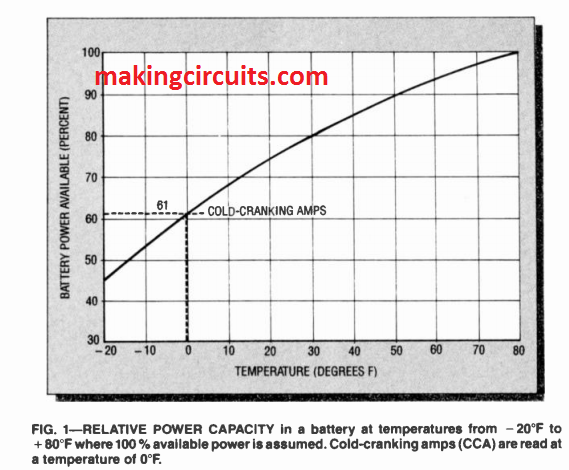
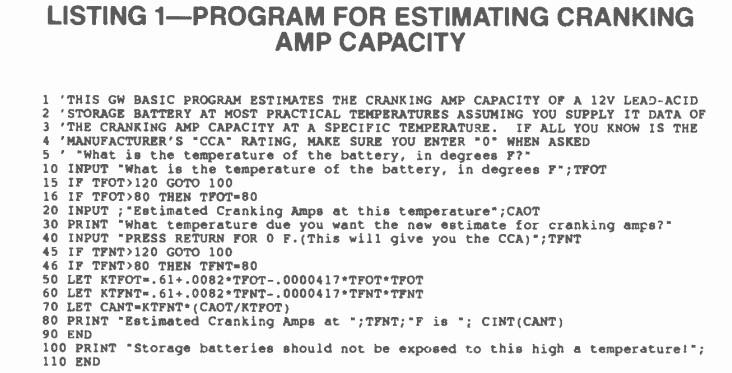
The BASIC system has the ability to determine the CCA of a battery at all typical ambient temperatures when the CCA at a given temperature is in hand. Both Fig. 1 and the BASIC system are according to General Motors Corp. studies. CCA estimator's depletion in your battery is simply a small 2.5 amperes, that makes it a lot more secure to work with than equipment which analyze the load.
Additionally, the circuit is not going to critically discharge your battery when it is utilized as instructed. Do not forget that the circuit is absolutely not an ammeter thus its measurements will simply present you with a sensible estimation of the potential CCA of the battery without essentially calculating it.
Once you've realized using this equipment, all that's necessary is a digital voltmeter and a thermometer to have you up to date on the status of your 12 volt automobile or motorboat battery if this includes a CCA rating from 150 to 1000.
Cold cranking amps
Cold cranking amps (CCA) is the value for the level of current a battery may supply for 30 seconds at 0°F without losing under a particular cutoff voltage. Figure 1 demonstrates that the battery power output increases substantially through 0°F to 80°F. Actually, a battery rated at 600 CCA (at 0°F) must be able to provide 1/0.61 x 600 or 984 cranking amps at 80°F!
An rough tutorial in figuring out the CCA rating for a battery which will start an engine without issues at 0°F relies on engine shift, generally tested in cubic inches. On the other hand, If your engine shift is measured in liters, you may multiply that number by 61 to obtain cubic inches in order to use the below information: An eight cylinder engine demands 1 cranking ampere per cubic inch of engine displacement.
As an example, to start an eight cylinder 350 cubic inch engine, the battery needs to supply 350 CCA. A six cylinder engine includes a CCA rating that may be 8 times the cubic inch displacement for each cylinder.
For instance, if a six cylinder engine carries a displacement of 231 cubic inches, the displacement for each cylinder is around 39 cubic inches. As a result, the battery will have to supply 39 x 8 = 312 CCA. A four cylinder engine carries a CCA condition that may be two times the engine's displacement in cubic inches.
For instance, in case a 4 cylinder engine carries a displacement of 180 cubic inches, the battery will have to provide 360 CCA. When the ambient temperature is persistently under 0°F, the battery must have a CCA rating which is 20% greater than that which could be determined for warmer temperatures. Besides CCA, you will find some other battery ratings in use these days.
For example, the MCA, for marine cranking amps, is a rating formulated for boat batteries that may be based on 32 °F rather than 0°F for CCA. An MCA rating for the equivalent CCA-rated battery is commonly 25 to 30% lower. An additional standards is reserve capacity, presented in minutes.
It identifies a battery's capacity to carry on delivering power to the engine and accessories when the car's charging system malfunctions. That test discharges the battery at a rate of 25 amp until the battery voltage falls from over 12 volts to 10.5 volts.
CCA for a 12 volt battery model
Many textual content exhibit a 12 volt storage battery equivalent circuit either being an great 12 -volt supply or as that source in series with a small resistance, maybe around 20 milliohms. An ideal voltage source comes with a constant voltage irrespective of current flow. It is able to supply limitless current and limitless power. Sadly, you cannot find any such thing as a possible ideal voltage source.
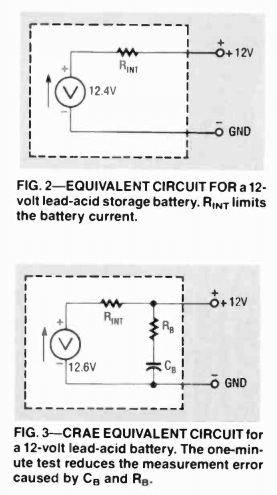
The equivalent circuit for a battery displayed in Fig. 2 above can be a acceptable design for the layout of a CCA meter. Having said that, a lot more reasonable equivalent circuit demonstrated in Fig. 3 incorporates a big capacitor and an extra resistor. That design deals with variations in battery output with regard to time.
A far more detailed model might consist of a time and current dependent voltage source along with time dependent resistors and capacitors. But, accounting for all these supplemental parameters would likely mess with the design of a straightforward, DIY meter.
Additionally, considering all those extra parameters may likely affect the precision of the meter.
How CCA Cold Cranking Ampere Circuit works
The CCA estimator purpose is usually to estimate the size of R(INT) as indicated in Fig. 4. You may find an inverse relationship between this particular resistor and battery capacity: the smaller the magnitude of R(INV) the larger is the battery's capacity.
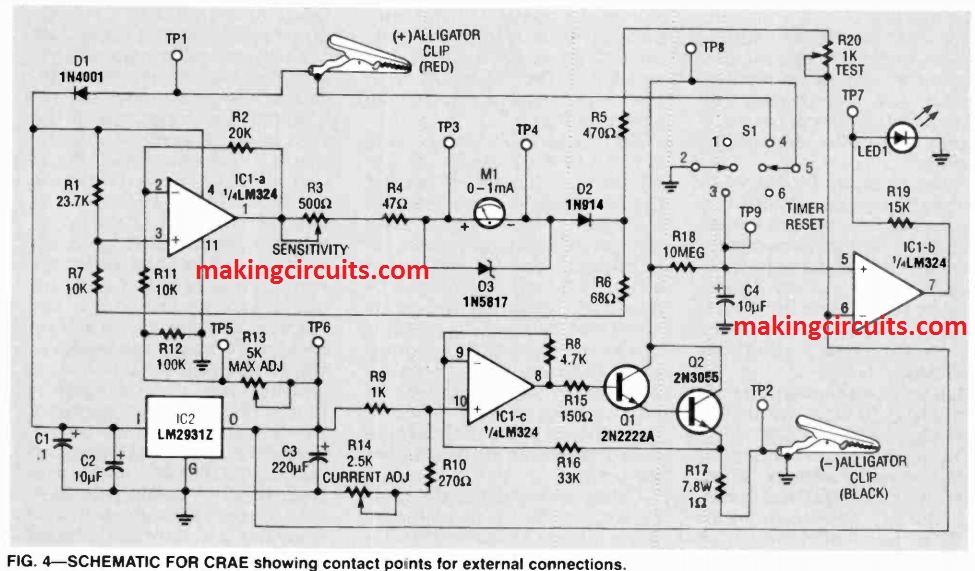
When CB and R13 are not present, R(INT) can quickly be approximated by adding a load to the battery, testing voltage and current, and then doing some computations.
The proposed cold cranking estimator circuit performs this for you automatically. However, it is initially important to discharge CE3 because the unit has to work with a timing circuit.
There are actually three primary stages in the circuit: The first, the voltage measuring circuit, is really a high gain voltmeter which reads a variable rate voltage from 11.9 to 12.5 volts.
The second stage includes a solid-state, constant current load which is fine-tuned to pull 2.5 amperes load irrespective of the voltage. The 3rd is a 60 seconds or so timer which illuminates an LED to reveal the measured readiness. The circuit which measures the voltage is made up of op amp IC1-a (1/4 LM324) hooked up in a differential amplifier circuit.
The voltage reference for this circuit is the 5 volt regulator IC2 (LM2931Z). Resistor R13, the MAX ADJ potentiometer, trims this reference voltage to increase voltage readings under absence of a load.
Resistor R3 is a PCB mount trimmer which sets current via the meter and it is a sensitivity control as shown in Fig. 4. Resistor R20 is a 1K PCB installed trimmer that adjusts the meter's zero point (0.05 milliampere). Resistors R5 and R6 increase the meter's negative terminal so that the the meter can be set at zero.
Diodes D2 and D3 safeguard the meter. and D1 helps to protect additional sensitive elements of the circuit from unintentional destruction when the test probes are first coupled to the battery. The main element of the constant current load is Q2.
When momentary two way toggle switch S1 is turned to the TEST position, current moves via Q1's emitter circuit since IC1-c supplies the base current. That emitter current in addition runs via Q2's base circuit, causing substantial current movement.
Resistor R17 each directly and indirectly regulates the constant current. As with any kind of transistor with an emitter resistor, Q2's current is actually constant simply because, as emitter current raises, emitter voltage follows.
Which means VBE and VcE are lesser in value, hence they tend to pull down the emitter current. However, this particular influence is not adequate to enable a constant current load. Op amp IC1-c accomplishes this job. Furthermore, ICI-c allows to deliver a close to ideal constant current load, and it additionally streamlines load current manipulation.
Inspecting the circuit diagram discloses that the op amp inverting input is linked by means of R16 to Q2's emitter. While Q2's emitter current goes up, the inverting input voltage of IC1-c goes up causing a reduced voltage output at pin 8 and lower current at base of Q1. This leads to a decrease in current at Q2's base and the ensuing reduction in Q2's collector and emitter current.
R14 tweaks the voltage on IC1-c's non-inverting input, and therefore adjusts the current by means of Q2's emitter. The timing circuit had been developed in order that the timing interval could change along with voltage.
(Smaller measurements on the attached meter are usually associated with low battery voltage and extended timing intervals.) This, to some extent, makes up for a totally charged (high open-circuit voltage) battery's inclination to exhibit relatively reduced CCA values compared to if it had been a little bit discharged.
The timing circuit is made of IC1 -b, C4. and R18. When S1 is in the TEST position, C4 begins charging by means of resistor R18. Once the voltage around C4 goes above 5 volts, the op amp's output turns "on" and illuminates the LED!
Construction
Probably the most high-priced part in this cold cranking estimator is the moving coil ammeter M1, equipped of indicating 1 milliampere. A customized PCB is not really needed since the design is a straightforward low frequency device, nevertheless it is likely to make the construction less difficult and quicker.
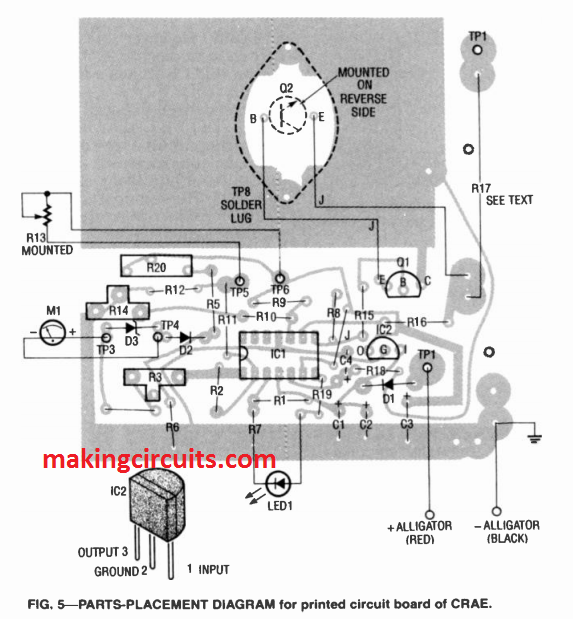
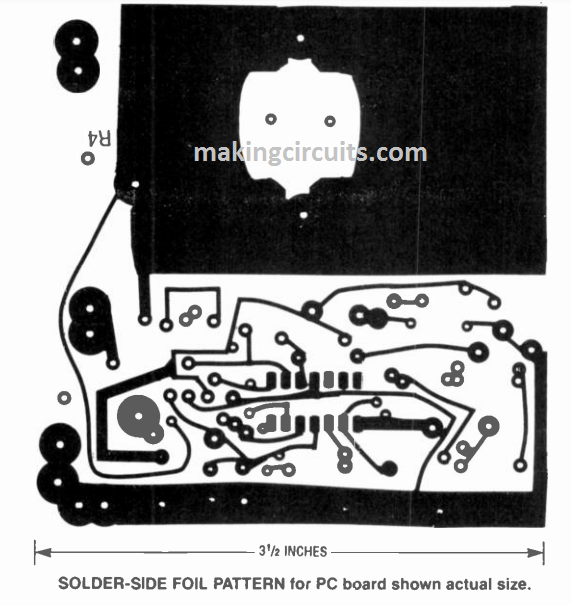
On the other hand, if you construct it quickly, make sure to put additional time in extensive testing and calibration. As per Figure 5. the component mounting tutorial, must be applied along with the circuit diagram in Fig. 4 while making the circuit to avoid complications.
Meter M1, switch S1, LED1 and potentiometer R13 are placed on the front panel of the cabinet; all 60 other components are installed on the PCB.
Be certain that the heat sink is in position while soldering Q2. The heatsink together with Q2 affixed is installed on the track side of the PCB.
On the component side, wires are hooked up from Q2's base and emitter to the PCB by using insulated jumper wires as demonstrated in Fig. 5. See that R17's power rating shows up in the list of parts as 5 to 7.5 watts.
Measurements suggest that the resistor have to dissipate 6.25 watts. Nevertheless, since the current typically moves periodically just for one minute each time, a 5 -watt resistor can be utilized.
You should definitely keep a minimum of a 3/8 -inch space between R17 and the circuit board to let air flow to get proper cooling.
Testing and calibration
Initially, adjust all potentiometers (R3. R13. R14, and R20) to their middle positions. Next, fix the output of a regulated power supply rated no less than 12.6 volts using a digital.
The specified voltage could be obtained from the middle wiper arm. Attach the positive alligator clip (red) to the supply's positive port and the other clip to the negative terminal. Do not operate the test switch during this period!
Slowly and carefully raise the supply's voltage for a 12.5 -volt display on the digital multimeter. Set R3 for a maximum (1 milliampere) reading on meter M1.
Now reduce the voltage to 11.9V and alter R20 for a 0.05 milliampere reading. Once again use 12.5 volts and alter R3 and/or R20 to get a 1.0 milliampere reading. Do this step again for 11.9 volts.
After a number of adjustments of R20 and R3. M1 should acknowledge 1.0 milliamperes in response to the 12.5 V on the alligator clips and 0.05 milliamperes when the voltage is 11.9 volts.
The multimeter must subsequently be employed to set R14 for a 2.5 ampere current by means of R17.
Hook up the associated alligator clips to a 12 V lead acid battery or a 12 V regulated supply which could supply a minimum of 5 amperes. (Make sure the red clip is attached to the + lead and the black clip to the negative lead.)
Next position the DMM's leads over the 1 ohm power resistor R17 and fine-tune R14 for a 2.5 volt reading on the DMM. This finishes the essential calibration of the cold cranking amp estimator circuit.
PARTS LIST
All resistors are 1/4 -watt, 5%, unless otherwise indicated.
R1-23,700 ohms, 1/4 -watt, 1%
R2-20,000 ohms, 1/4 -watt, 1%
R3-500 ohms PCB trimmer
R4-47 ohms
R5-470 ohms
R6-68 ohms
R7, R11-10,000 ohms
R8-4700 ohms
R9-1000 ohms
R10-270 ohms
R12-100,000 ohms
R13-5000 ohms potentiometer
(panel -mount)
R14-2500 ohms PCB trimmer
R15-150 ohms
R16-33,000 ohms
R17-1 ohm, 5.0 to 7.5 watt
R18-10 megohm
R19-15,000 ohms
R20-1000 ohms, PCB trimmer, 15
turn
Capacitors
C1 -0.1µF, 25 volts
C2 -10µF, 25 volts, electrolytic
C3 -220µF, 16 volts , electrolytic
C4 -10µF, 25 volts +1- 10%, tantalum
Semiconductors
IC1-LM324 quad op -amp
IC2-LM2931Z 5 -volt voltage
regulator
Q1 -2222A NPN transistor
02-2N3055 NPN transistor
LED1-Light-emitting diode (High - efficiency GaAsP on GaP)D1-
IN4001 silicon rectifier
D2 -1N914 silicon diode
D3-IN5817 schottky barrier rectifier
Other components
S1-DPDT momentary action with
off at center
Ml-Panel meter, moving coil, 0 to 1 mA.
Miscellaneous: two alligator clips
(1 -inch jaw length), two lengths of
two -conductor parallel flexible 18
AWG stranded copper lamp cord
with PVC or rubber insulation (approx. 3 feet long), PC board,
case-Radio Shack Cat. No.
270-232 or equivalent, control potentiometer knob, aluminum heat
sink, LED mounting hardware
insulated hook-up wire, solder,
etc.
Leave a Reply