Despite the fact that SPWM are typically deemed the simplest way of replicating and enacting a moderately pure sine waveform, the point that it will probably not emulate or overlap with a real sine wave causes the design to be somewhat elementary, especially when judged against a Multi Level cascaded sine wave inverter theory.
We are able to evaluate and investigate the two sorts of sine wave simulation principles by looking at the following graphics:

You can easily identify that the Multi level cascaded principle generates a far more noticeable and effectual demonstration of a real sine wave compared to the SPWM idea which counts entirely on coordinating the RMS significance with the primary sine wave level.
Developing a standard Multi Level Cascaded sine wave Inverter can be hugely challenging, however the theory which is discussed below allows the application more convenient by employing common ingredients.
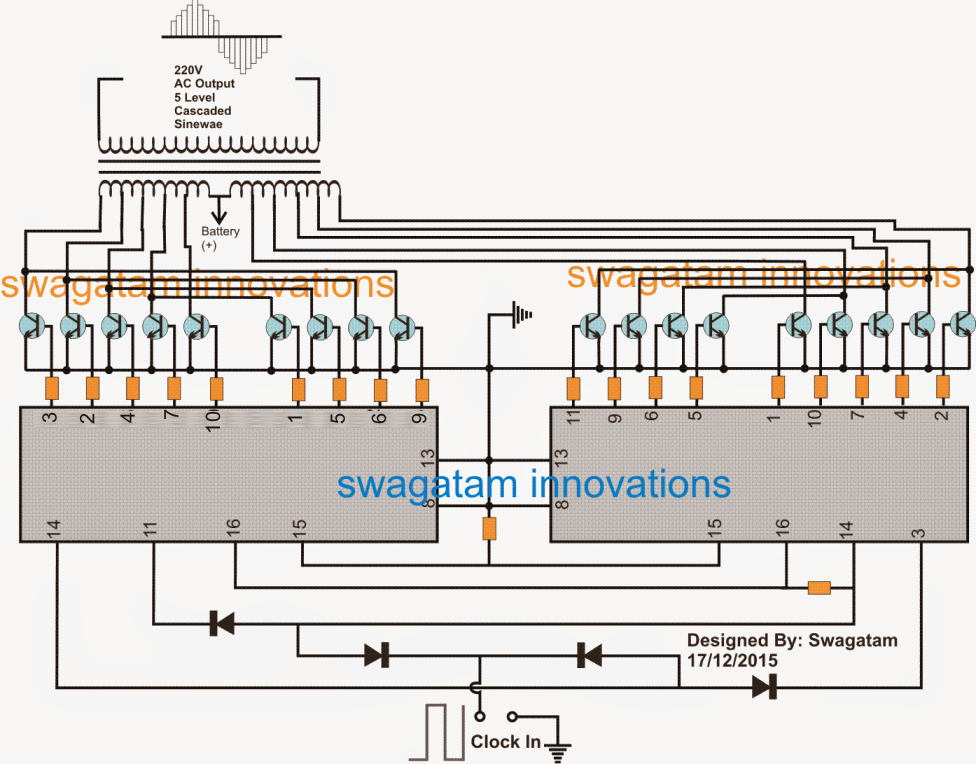
Multi Level Cascaded Sine Wave Inverter Circuit
Parts List
All resistors are 10k, 1/4 watt
All diodes are 1N4148
All BJTs are TIP142
ICs are 4017
With reference to the figure above, we are able to observe just how easily the multilevel cascaded inverter principle may be realistically enforced by means of just a muti-tap transformer, a few 4017 ICs and eighteen power BJTs, which can be readily swapped with mosfets if desired.
At this point a couple of 4017 ICs that happen to be Johnson's 10 stage counter divider chips, are cascaded to churn out a sequentially moving or following logic highs across the outlined pinouts of the ICs.
These sequentially moving logic are utilized for activating the associated power BJTs in an exact progression which subsequently switch the transformer winding in a manner which then causes the transformer to construct a cascaded design of sine equivalent waveform.
The transformer makes up the core of the circuit and engages a specifically wounded primary with eleven terminals. These terminals are simply taken out uniformly from one extended worked out winding.
The BJTs connected with one of the ICs trigger one of the halves of the transformer by means of 5 taps making it possible for the procreation of multi level rectangles, constituting one half phase of the AC waveform, at the same time the BJTs in connection with the second ICs performs the parallel operation to structure up the lower 50% AC cycle through a 5 level cascaded waveform.
The ICs are powered by clock signals put on the shown state in the circuit, that can be procured from any regular 555 IC astable circuit.
The initial five units of the BJTs develop the five numbers of the waveform, the remaining four BJTs transform the corresponding in opposite sequence to accomplish the cascaded waveform obtaining an overall of nine skyscrapers.
These skyscrapers are produced by bringing forth an climbing and diminishing voltage stages by the switching of the interacting winding of the transformer which happen to be calculated at the appropriate voltage ranges
For instance, winding #1 could possibly be calculated at 150V with reference to the central tap, the winding #2 at 200V, winding #3 at 230V, winding #4 at 270V as well as winding #5 at 330V, therefore when these are flipped in sequence by the range of the indicated five BJTs, we obtain the initial five numbers of the waveform, after that as these winding are powered in opposite by the following four BJTs it results in the sinking 4 level waveforms, consequently implementing the top part of the half cycle of the 220V Alternating current.
The identical is duplicated by the alternative nine BJTs involved with the other 4017 IC contributing to the lower half of the five level cascaded AC, which accomplishes 1 full AC waveform of the preferred 220V AC output.
Transformer Details:

As could be spotted in the earlier mentioned plans, the transformer is a traditional iron core variety, manufactured by winding the primary and the secondary using winding equivalent to the suggested voltage taps.
Whenever linked with the matching BJTs these winding could be anticipated to generate a five level or an overall of nine number of cascaded waveform in which the initial 36V winding may well correspond and stimulate a 150V, the 27V may well trigger the exact same of 200V, while the 20V, 27V, 36V could well be committed of causing 230V, 270V and 330V across the secondary winding in the presented cascaded structure.
The group of taps on the lower hand of the primary may well implement the changing over to finish four ascending amounts of the waveform.
An equivalent operation may be replicated by the nine BJTs in connection with the interrelated 4017 IC for developing the negative 50% sequence of the Alternating current...the negative is provided on account of the reverse adaptation of the transformer winding with reference to the middle tap.
Hey Swagatam :¡¿did you really have build a multilevel like this with mosfet?
are you joking? when you turn on the mosfet with lower turns respect the middle of the transformer on the taps with more turns of the same side you have negative voltage wich will be shortened by the paralel diode intrinsic of the mosfet of this side !!!!!!!!!!…..a very well done short circuit………..
the only way its the use of a bloking diode ( and its voltage loss wich may be takened in account when you calculate the transformer turn ratio ).
Or a bidirectional switch .(every word of mine have been chequed on the bench with real inverters……… and not virtual )
you can connect diodes across the mosfets or the BJTs for that which I did not show here. It is the concept that has been discussed, any sensible person will understand and implement extra precautionary measures that may be needed for evading a possible issue…nobody said that this an efficient design, rather a low cost method of getting stepped sine wave.
probably im a to much sensible person ……. and for this reason I prefer clear things , and precise words .
after all this chat , i like to tell you that i prefer the same concept but with bilateral switch on the secondary side connecting diferents taps .
In this way we have a square wave on primary and you can give the shape that you want depending of the sequence connection switch.
the primary aproach must be implemented with bilateral switch because if you have reactive loads (inductive) current lag , you will discover a very pretty spikes due a situation of open switch . probably this thing will be not easy to see at first sight.
regards
a very sensible
OK the idea makes sense, it could be done through optocouplers for switching the secondary side devices and these devices could simply be triacs, no need of special bilateral switches.
the primary side could be switched through a full bridged square wave, while the secondary side taps using sequentially switching triacs.
yes indeed , but try to load with a motor or a inductive load ( ihave done ),instead bilateral switch will not suffer of the latched condition of a tyristor or triac (because there is a lag current appears short circuit between them , you start a second one while the other its still conducting ) with resistive loads the waveform could be shaped at your wish , ihave working a 3kw inverter with 4 taps on the secondary (chooosed to the closest value of a sinusoidal wave at each degree of the function ) and each half cycle of the 50 hz voltage has shaped with 8 steps (16 steps for a complete cycle of 20 ms )
the waveform its so good !! the inverter its very strong…….remember we have the patagonia with places where the closest person could be at 200 km we must design very conservative electronics,…just on the opposite sense of the common way !!!!
yes Inductive loads can be tricky, so bilateral switches using IGBT/mosfet will be a better choice, I’ll try to design it roughly and present it here soon.