I have already tested and have confirmed the advantages of using pulse charging with Ni-Cad batteries. I've tried pulse charging to desulfate lead-acid batteries only once the plates were so terribly sulfated, so I could easily take a chance.
Pulse charging can knock down the sulfation in lead acid batteries, however I have so far never seen a battery in sulfated condition which comes back convincingly. Additional strategies I have experimented with offer far better effects.
So I don't recommend, under any circumstances using pulsed charging for lead acid batteries.
Actually you may find it shocking that lead-acid batteries dislike the pulse charging technique, given that many car alternators enforce a half-wave charging cycle with extensively fluctuating frequency over a large to substantial load current.
Pulse Charging Method
When we talk about sealed 'maintenance -free' (MF) lead-acid batteries particularly, choosing whether or not to apply pulse charging is immaterial, because you cannot look at plates.
Several alterations on the inner structure for MF batteries imply that sulphation is `natural'.
Therefore efforts to restore this type of battery might ruin an absolutely functional battery. SMF batteries have huge applications fields, such as in UPS, power supplies for example, as well as for alarm systems.
Charging process
A completely discharged (<10.8V/6 cells) battery may quickly start forming sulphate crystals. If charged from a constant voltage source, the sulphate will hinder satisfactory current circulation to convert the sulfation back.
The details in the manufacturer's datasheet is rather crystal clear: when the battery is not kept discharged over a couple of weeks, boosting the charge voltage to around 30V/6 cells may knock down the sulphate crystals.
The charging source should be current controlled. I discovered that around 25 % of the 1 Ah capacity performs nicely. As the terminal voltage drops to 10-8 V per 6 cells while the sulphation eliminates and plate charging initiates, which allows a comfortable trigger limit.
The datasheet shows that this is the ideal level where the constant-current charging must be switched to constant-voltage charging. The right charging voltages are: normal lead-acid (with caps on top) 14.4V, MF (sealed maintenance free etc.) 16-9V.
The Right Charging Procedure
The correct charging technique that I've been working with to revive these types of dead batteries consists of a table-top oven heater element. The oven element limits current between 1.75- 2-5A determined by its temperature.
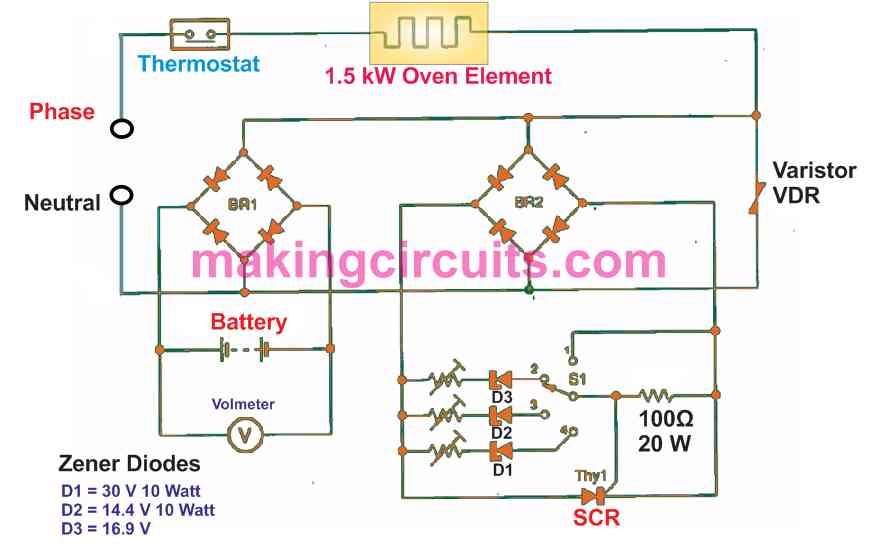
Because this current is comparable to that necessary to service-charge MF batteries, I introduced a bridge rectifier, BR1, at the neutral supply input. Using this type of primitive circuit arrangement, the best method of manipulating the constant-voltage phase of the charging demands the use of a large zener diode.
The best suitable device I could imagine could be the one utilized on English motorbikes. These are generally even now that are available and, I believe, resemble the Philips BZY91-C15. It could be preferable to employ, if easily obtainable, a 16.9V regulator diode of the same power rating to safeguard against maintenance free type batteries from gassing their electrolyte away, simply because they cannot be capped up.
I no longer worry about voltage control for standard lead-acid batteries, I simply allow these to get charged on current-controlled DC input until I find the cells have started gassing.
These can topped up anytime using distilled water just before using them. Another solution is to apply a second bridge rectifier and a thyristor crowbar to quit charging at the intended full charge voltage level.
Each bridge rectifiers should definitely be rated to handle the maximum current of the oven element at the start when the element is cold.
Calculating the Zener Diode
While calculating the zener voltage necessary, the two bridge rectifiers cannot be believed to have identical voltage drops, considering that BR1 is transporting all the current and BR2 probably none until the SCR actually fires.
Selecting the Thyristor (SCR)
The SCR's firing limit voltage should be as well evaluated. Therefore it's not just about including a forward-voltage restriction. The voltage crowbar can limit with a per half -cycle schedule hence, when the battery terminal voltage due to any reason drops under the preset trigger voltage, the crowbar is going to be cut-off, enabling the charging process to initiate again, until the terminal voltage goes up again over the SCR trigger voltage.
The Correct Desulfation Voltage
The genuine desulphating voltage is indicated in the datasheets as 29 V. As it may be feasible for a intensely sulphated yet recoverable battery to arc internally if an increased voltage is fed, another SCR circuit could be included around BR2 to stop any voltage greater than 29-30V applied to the battery.
In case battery desulfation doesn't start off at 30V from the circuit, there may be no risk in trying disabling the 30V crowbar and let the higher voltage go in. However a battery in such terrible condition might never recover to its 100 % capacity.
To reduce heatsinks and costly thyristors, an single-pole-four-way switch could be applied to select
- No voltage limitation,
- 30V limitation for vendor certified desulfating therapy,
- Lower restriction for charging standard lead-acid batteries at 14.4V, and
- An increased limitation for charging MF/NPO batteries at 16-9V.
As is visible in the circuit diagram, the three controlled selections hook up the SCR's gate to a zener diode in series through a adjustable preset or pot.
The gate-shunted location is the "gloves-off" setting for seriously sulphated batteries. In this switch position, your battery might get permanently fried or just get a few breaths back, therefore do not count on the battery to recuperate to its optimal rated capacity.
The voltage-dependent resistor (VDR) is incorporated to defend the SCR and the rectifiers from thermostat switching voltage spikes.
Advanced High Voltage Spike Method
In the following section we discuss the actual advanced method of implementing battery desulfation using high voltage spikes, which is derived from the battery voltage itself.
What is the actual definition of sulphation? It is a situation when the lead sulphate on a battery's plates during discharge undergoes structural modifications. Sulphate crystals of a reasonable size develop, blocking the porosity of the lead plates and reducing their range of operation. The battery's capacity is diminished as a result, and it can no longer deliver significant currents or be charged successfully in the traditional manner. When a sulfated battery is charged, conducting bridges (short circuits) form between the plates, which were previously considered to be impossible to remove. It signaled the battery's service life was coming to an end.
Popular Techniques
You won't instantly bring a worn battery to the recycling store in the genuine spirit of electronics aficionados. They're not cheap after all, and it's worth making sure it's truly at the end of your bagpipe. Insiders are certainly familiar with certain methods that pin a weary battery.
One of the most famous is the repetitive battery charging and unloading. This approach leads to the restoration of much of the lost capability for a certain reason. In some situations, the use of big current pulses seems to have some impact on a regular basis. However, in instances when poor sulfate batteries must be restored to life, both methods leave something to be requested.
Remedy
Several manufactures have developed ways for sulfation reversal in lead acid batteries in recent years with different successes. Some pulsed charge appears to be the basis of the working processes. This is contrary to ordinary charging techniques with a steady voltage in most cases. The newest approaches for revitalizing platinum-acid battery are presented here.
The desulfator circuit a gadget that feeds the battery regularly with brief yet hard pulses whilst it discharges slightly between the pulses. As far as we know, this is the most efficient technique of breaking down undesirable sulphate crystal deposits and restoring the battery plates to an acceptable level. As the energy needed for the charging pulses is derived from the battery itself (this may at first appear somewhat strange, but also from the charging of the battery), it is recommended to use the battery and the desulfator circuit in parallel if the batery remains with a very small capacity – we'll go into that in detail later.
We must be realistic here and acknowledge that our own circuit experience is not adequate to ensure that it operates well without condition. However, given that the circuit is not very costly, usage of it is in the interests of uncertainty.
Using High Voltage Pulses
The electronics required for the desulphator may be seen from the circuit schematic in Figure 1.
The circuit comprises two parts: a generator that generates the pulses of charging, IC1, IC2d and T1, and a circuit indicator composed of just over three opams (IC2a, b, c) and three LEDs that indicate the condition where the battery is.
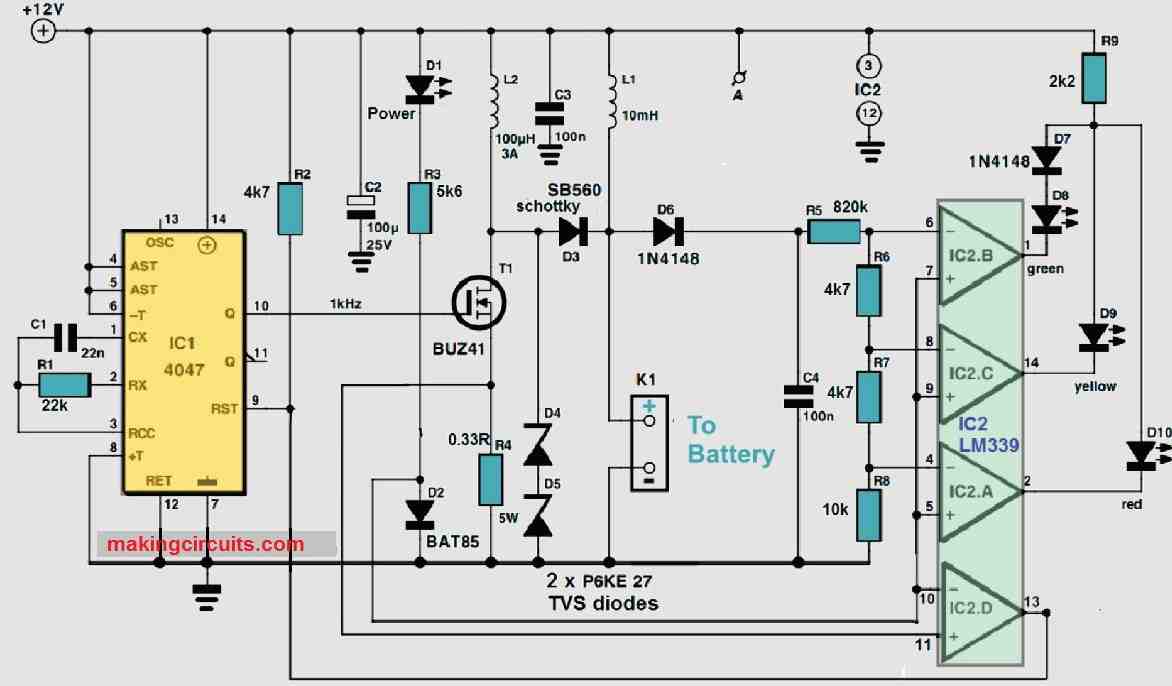
Let's start with the pulse generator. It, like the rest of the circuit, gets its power from the battery through K1. While we're on the subject of power supplies, they should have a reasonably steady voltage and be devoid of spikes (besides the ones produced by the circuit itself). To eliminate unnecessary spikes, suppressor inductor L1 has been added, alongside reservoir capacitors C2 and C3.
When the supply voltage is present, LED D1 illuminates. Continuing with the pulse generator, IC1 (a 4047) generates a square wave with a frequency of 1 kHz and a duty cycle of 50%. FET T1 will switch on immediately when the Q output of IC1 turns high. This enables a (discharge) current to travel from the battery via L2, increasing linearly until the voltage across R4 is approximately 0.35 V; the current is subsequently approximately 1 A.
The comparator IC2d will swap over at that point, allowing IC1 to reset and T1 to switch off. The magnetic energy stored in L2 is now transformed into a voltage spike and supplied to the battery through D3. The magnitude of the spike is determined on the battery's condition. As long as the battery is in good condition and has a low internal resistance, the maximum spike would be small as well (lower than 15 V). The peak might be as high as 50 V when the internal resistance is strong. The pair of series linked zener diodes, D4 and D5, restrict its maximum value.
As the battery status may be measured by the magnitude of the rechargeable pulses, a simple circuit is included that shows the pulse's peak value. The three IC2a-c comparators evaluate the peak value of C4 and turn on at 15, 20 and 30V. If the battery is rather excellent, the green LED (D8) light up. The yellow LED (D9) has a medium battery and the red LED is a pretty bad battery (D10).
How the Indicators Work
Details on the indication circuit must be discussed: to avoid illuminating all three LEDs simultaneously at extreme high peak voltages, they were connected in parallel to a common series resistor (R9). Since the red LED's voltage is less than the yellow LED, it never lights up simultaneously. The identical voltage drop on the yellow and green lamps does not illuminate here, and that's why the green lamp has a conventional diode (D7) hooked up in series to it. This technique does not work here.
How to Use
The desulfator circuit may be utilized in three distinct ways. The first is for the prevention of sulphation on a battery with little, or no, sulfur in an existing system (for example in a car). By physically hooking up the circuit to the battery with the shortest practicable connections, it is incorporated into the system. Because the circuit is irrevocably coupled, nothing further must be done. There are around 20 mA of current usage, thus the battery may unload if the battery is not sometimes charged.
Restauration of sulfated batteries can be accomplished in two methods. First, the battery must be loaded, the charger removed, and the revitalizer then connected. Since the battery itself extracts the energy for charging pulses it will drain slowly. This procedure must be constantly monitored as a battery must be totally drained promptly. In fact several loading/unload cycles are likely to be needed before a poorly sulfated battery may recover.
Since the preceding procedure takes great care and risks leaving the battery needlessly in a drained condition (which is hazardous for a leadacid battery!), the next technique is probably better. With a trickle charger linked in parallel, the battery is hooked up to the desulfator circuit . There is thus no charge that gives 7 A or greater current but a current that offers a maximum of 1 or 2 A. This can be continually linked without issues to the battery.
very useful website, I have been looking for a website for a long time to learn something about desulfurization of batteries, and how to make a device that can be done thanks to my best regards
Thank you so much….
Hello Admin of MakingCircuits.Com,
This is more of a general comment. Are there any current day on the market Desulfators that mimic the behavior of your proposed charging Desulfation Car Battery Revival method?
If not are there any that are even “remotely” close or use some of the techniques that utilize 50% or up to 90% of the desulfating techniques you are recommending to be effective?
Lastly, could you yourself build a “safe” consumer prototype model for people to test out your method and even buy this model from you if it is actually superior to what is out there on the market?
Nice detailed write up. I’m not an EE but my father was and I’m sure he would have understood everything outlined were he still around. As a multi decade computer technician and now recently learning how to take apart a car engine to clean out the entire EGR and PCV system. Then finally putting it all back together the one remaining culprit after cranking and not starting intermittently was the old 2008 Car Battery that had been working until 2022 through plenty of babying seemed be the reason. That led me to search around on other battery revival techniques. I did use a 2012 BatteryMinder on another new battery for a different vehicle just to maintain its capacity as close to brand new as possible but I do not believe even that could revive a 14 year old car battery above 12.10V to 12.90V where it would be closest to peak condition.
Is there a device out that that accurately measures a car battery’s current amp capacity? If not could you build something like this as an independent tool or even combine it to your Desulfator prototype so it would show Current Voltage, Current Amperage Capacity and an Estimated Total Amperage Capacity of the battery? That way you can see the before and after effects in real time when applying your Desulfation method to a completely drained battery or one that is drained slightly below cranking potential that can still be revived. The only method I can check on a battery is just the Voltage which doesn’t actually provide the actual batteries remaining amperage. Even if the voltage shows 12.40V initially and after cranking and not starting the voltage drops down to 12.14V so it is obvious “Voltage” doesn’t’ tell the whole story of how much actual amperage the car battery actually has which is a more accurate indicator of its health.
Thank you.
Hello J.C.
I am sorry, I do not seem to have the answers to your questions, because my knowledge about desulfators is not very good. Also, unfortunately it is not possible for me to build a prototype for you.
Maybe in that point, you should given credit to homemade circuits and Swatagam…